CNC tube benders are an essential tool in industries like automotive, aerospace, and furniture manufacturing, where precision tube bending is critical.
What Is a CNC Tube Bender?
A CNC (Computer Numerical Control) tube bender is a machine that automates the process of bending metal tubes and pipes to precise angles and shapes. It uses programmed instructions to control the movements of the machine, allowing for repeatable, accurate bends without manual intervention.
Unlike manual or hydraulic tube benders, CNC machines can handle complex shapes and high production volumes with little human input. At Haden, our CNC tube benders are designed for durability, speed, and precision, making them ideal for industries where efficiency and accuracy are crucial.
The Basic Components of a CNC Tube Bender
A CNC pipe bender consists of several key components:
- The Clamping Mechanism: Holds the tube securely in place during the bending process.
- The Bending Die: Shapes the tube to the desired angle. Different dies are used for different bend radii.
- The Mandrel: Often inserted inside the tube to prevent it from collapsing or wrinkling during the bending process.
- CNC Control Panel: This is where the operator inputs the specific angles, bend radii, and instructions for the machine to follow.
Each of these parts works together to ensure that the tube is bent with high precision, regardless of the material or complexity of the bend.
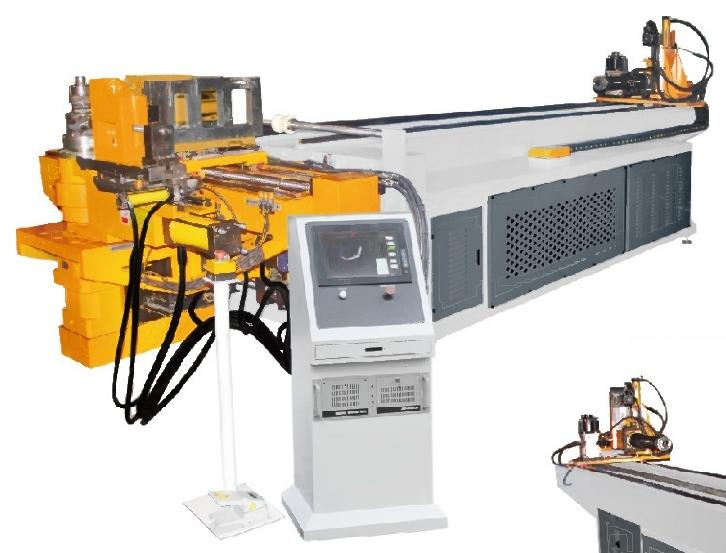
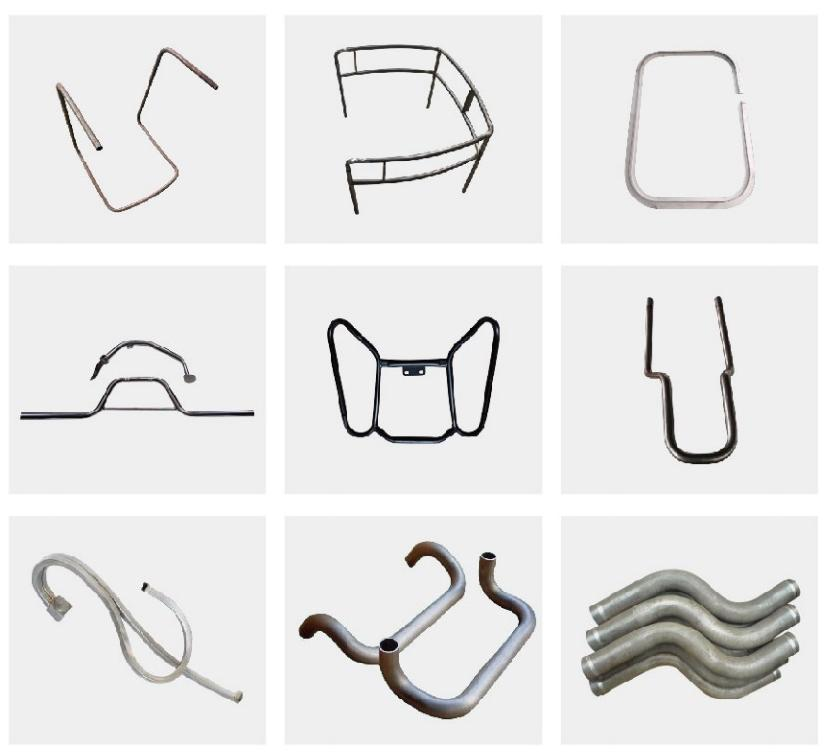
How CNC Tube Bending Works
The process of bending a tube using a CNC tube bender follows these steps:
- Tube Positioning: The tube or pipe is loaded into the machine and clamped securely in place.
- Programming the Bend: The operator inputs the specific parameters for the bend into the CNC system, such as the angle, radius, and rotation.
- Bending Process: The bending die rotates around the tube while the mandrel and clamping mechanism work together to shape the tube without causing any distortion.
- Unloading: Once the bend is complete, the tube is unclamped and removed from the machine, ready for inspection or further processing.
Thanks to the precision of CNC programming, each tube is bent exactly to the specified angles, with little variation from one part to the next, making it perfect for large-scale production.
Types of Bends CNC Tube Benders Can Achieve
CNC pipe benders are capable of performing various types of bends, including:
- Simple Bends: Single-angle bends, typically at 90 degrees or less.
- Compound Bends: Multiple angles bent into a single tube.
- Rotary Draw Bends: Precision bends with a fixed radius, often used in automotive and aerospace applications.
- Roll Bends: Bends that curve over long sections, ideal for creating large-radius curves.
The versatility of CNC machines allows for intricate designs and the ability to work with different tube sizes and materials.
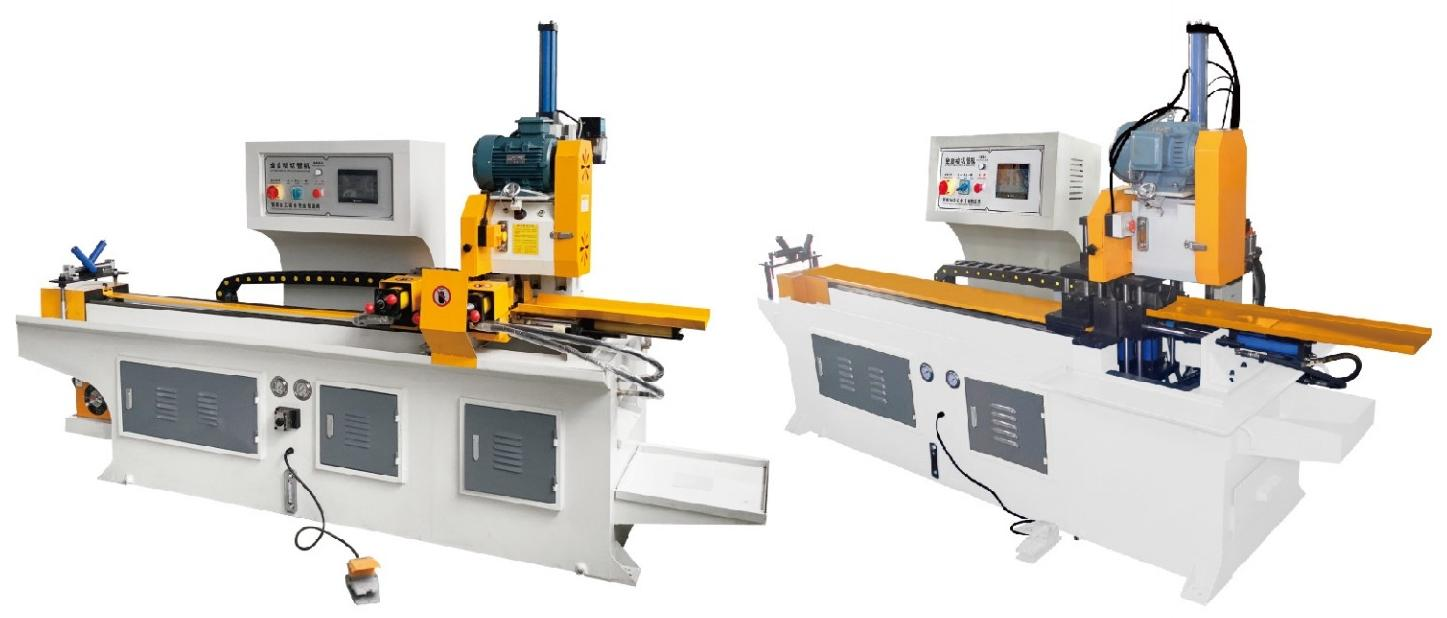
Advantages of CNC Tube Benders
The benefits of using a CNC tube bender over manual or hydraulic options are significant:
- Precision: CNC controls allow for repeatable, exact bends every time, reducing waste and ensuring consistency.
- Efficiency: Automation speeds up production and reduces human error, making CNC benders ideal for high-volume operations.
- Flexibility: CNC benders can handle complex shapes and multiple bend types in a single run.
- Material Handling: CNC tube benders can work with a wide range of materials, including stainless steel, aluminum, and copper, allowing for more versatility in manufacturing.
At Haden, our CNC tube benders combine advanced technology with user-friendly controls, enabling even operators with minimal experience to achieve perfect bends.
Common Applications for CNC Tube Benders
CNC pipe benders are used across a variety of industries, including:
- Automotive: To create precision exhaust systems, roll cages, and fuel lines.
- Aerospace: For bending complex tubing used in aircraft structures.
- Furniture: To form metal tubing for chairs, tables, and other furniture frames.
- Construction: In bending handrails, metal supports, and piping.
The versatility of CNC tube benders makes them an indispensable tool for any business working with metal tubing.
Conclusion
If you’re in the market for a CNC tube bender, understanding how these machines work is key to choosing the right one for your needs. From high-speed production to unparalleled precision, CNC benders offer significant advantages over traditional methods. At Haden, we pride ourselves on offering high-quality, efficient CNC bending machines that help you meet your production goals with ease. Whether you’re in automotive, aerospace, or construction, our CNC tube benders are built to provide reliable, repeatable results.