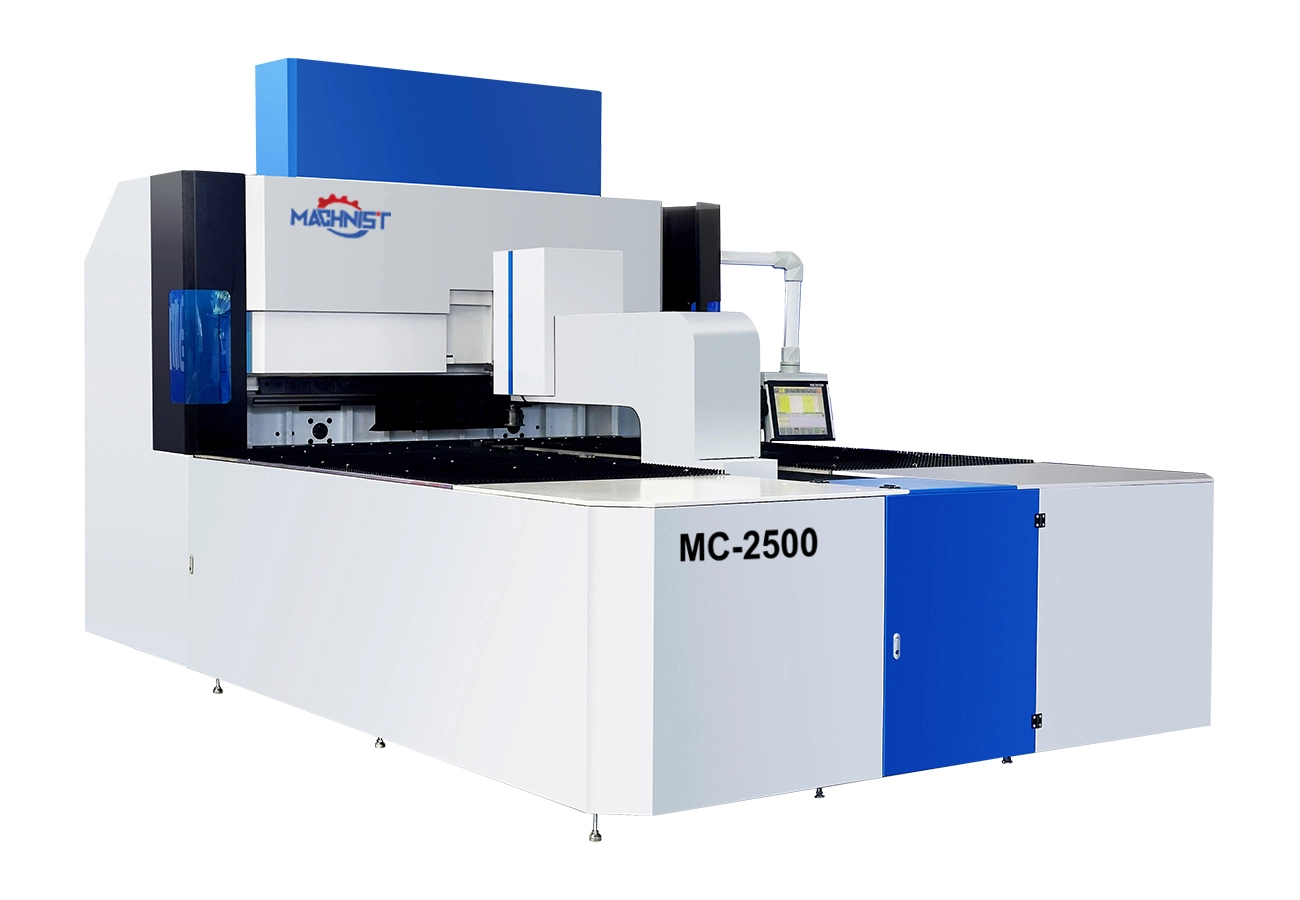
Design Adherence to High-Precision Standards
The entire machine is meticulously designed and manufactured in accordance with high-precision machine tool standards, ensuring a commitment to quality and precision.
Quality Materials and Rigorous Inspection
The main bed is constructed from high-grade castings, and both castings and welding parts undergo strict inspection procedures, emphasizing the use of quality materials and meticulous craftsmanship.
Stress Relief and Integrated Processing
Employing a special stress relief process and high-precision machine tools for integrated processing, the machine ensures optimal stability, accuracy, and high rigidity.
Final Inspection with High-Precision Detectors
The final step involves the use of high-precision detectors to strictly control the machine, guaranteeing long-term operational accuracy, strength, and overall stability.
Applicable
New energy, home appliances, electricity, western kitchens, elevators, communications, cabinets, medical machinery, and home furnishings
Feeding method
Suction cup Pressure arm
Material requirements
Flat, corrugated, mesh, hollow

Capacity
Width: 1000-3200mm
Thickness: 0.3-3mm Height:150-300mm Control Axis: 9-11
Feature
Automatic mold change
Upgrade
Robotic arm, automated workshop.offline programming
What services we provide
Precision Bending
Versatile Applications
High Efficiency
User-Friendly Controls
Durable Construction
How we work
Design
Manufacturing
Assembly
Testing
Training
Application industry
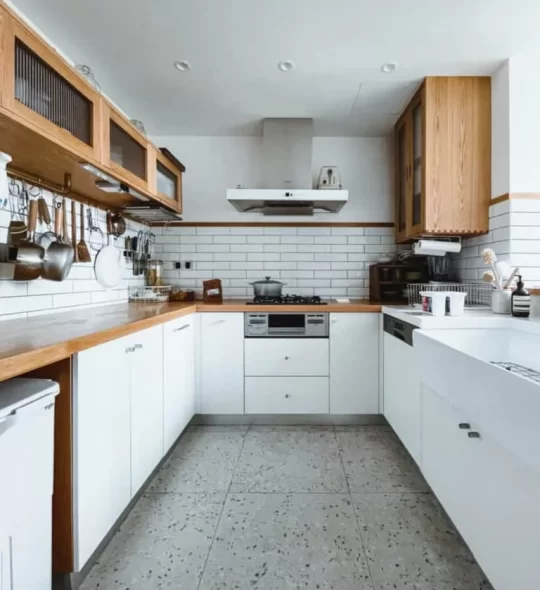
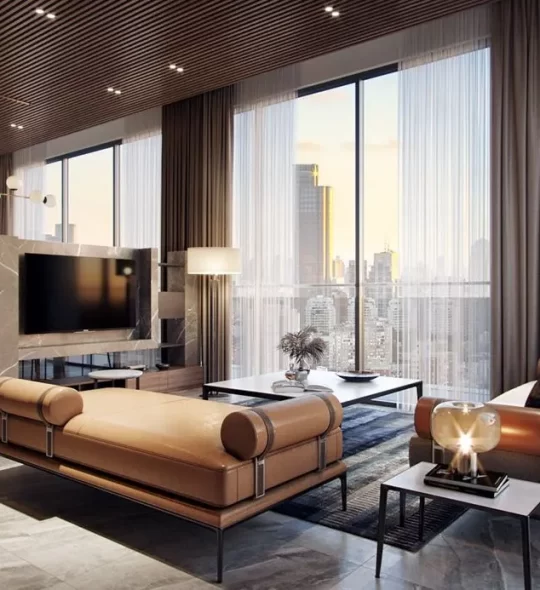
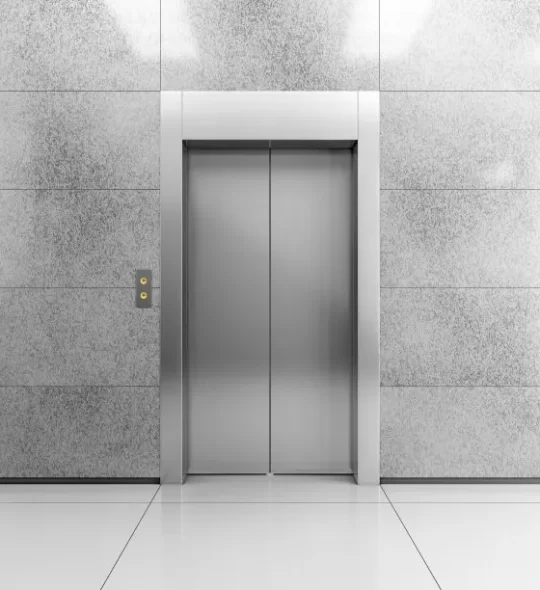
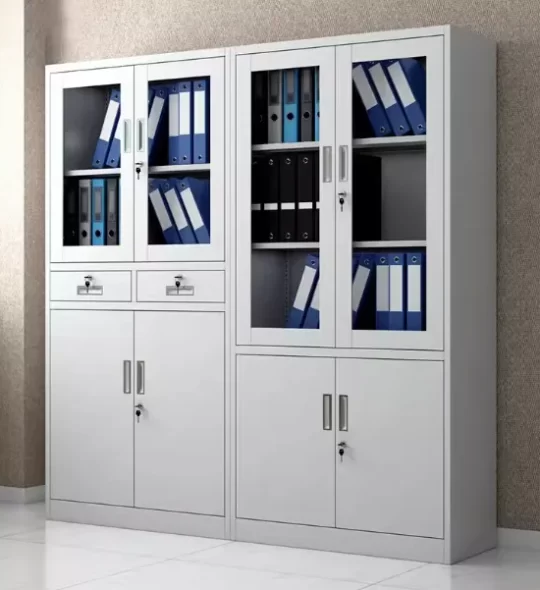
In the sheet metal industry, the panel bender is a key tool for efficient and precise bending of metal sheets. Its automation reduces manual work, ensuring consistent, high-quality products like enclosures and panels. The panel bender significantly enhances production efficiency, making it a vital solution for sheet metal processing.
Panel bender features & sample
- High -grade cast in one body
- Multi axis concurrent linkage control system
- C series 9 axis, A series 13 axis standard,also can be customized
- C axis lifting (Optional)
- Double C-axis automatic following system (Optional)
- Graphical visual error detection programming
- Self-lubricating oil supply systemDouble Y-U automatic positioning guiding ruler (Optional)
- Anti-mislaying detection function of workpiece ( Optional)
- Custom function of workpiece precision surface
- 0.001mm system accuracy
- Partialloaddetection system
- Plate thickness measuring system
- Off-load bending following system(Optional)
- Interchangeable and customizable narrow module (Optional)
- Cloud operation and maintenance management interface
- Y axis double base ruler (Optional)
- Offine editing function
- Big data self-learning function
- Advanced programming capabilities
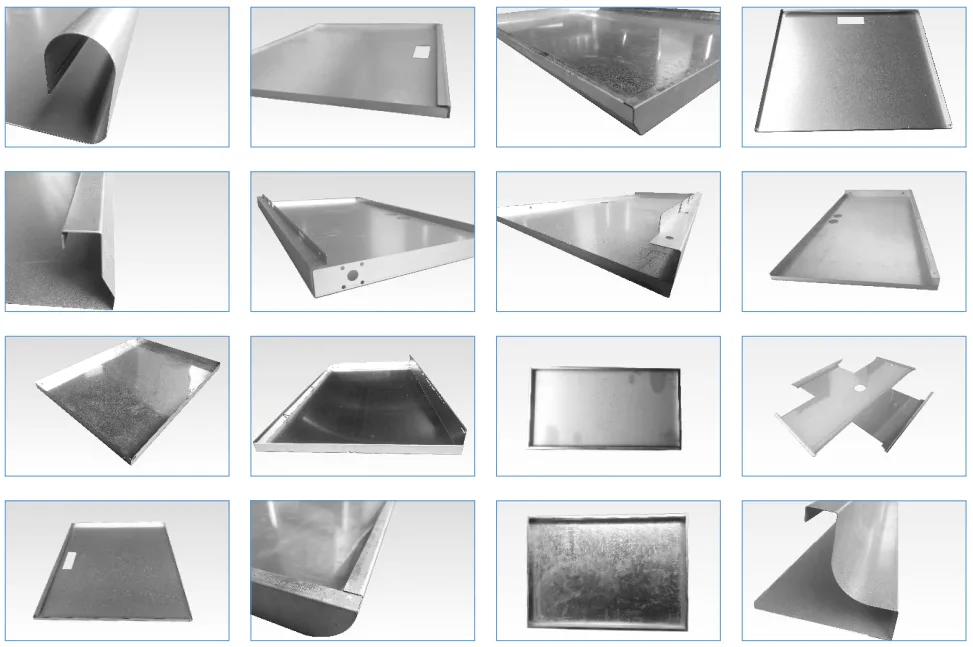
- Upper and lower dead edge function
- Flattening function
- Automatic assembly for self-drive loading and unloading
- The handwheel function
- High speed control module
Processing Equipment
- Our hydraulic NC&CNC press brake epitomizes our manufacturing prowess, seamlessly blending technology and craftsmanship.
- With precision and efficiency, this cutting-edge machinery showcases our commitment to high-quality metal fabrication, reinforcing our industry leadership.
Configuration
Machine Bend
Meticulous Machining for Bed Precision: Precision in the bed is achieved through careful and detailed machining, ensuring accuracy in every aspect of the machine.
Comprehensive Annealing for Deformation Control: To minimize deformation and guarantee accuracy, the entire machine undergoes comprehensive annealing, a crucial step in maintaining structural integrity.
High-Grade Core Frame with Stability Assurance: The core frame, crafted from high-grade QT500-7 and gray iron 250, undergoes thorough testing. Precise finite element stress analysis and a stable triangular interconnection design ensure safety and stability, especially under high-tonnage impact forces.
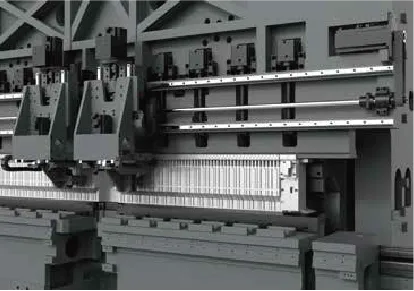
Automatic Tooling Change
Automatic Tooling Change Algorithm: Exclusive patented algorithm for seamless tooling changes.
Partial Bending with Assistant Tooling: Precision in partial bending with dedicated assistant tooling.
Small Batch/Varied Types Production: Tailored solutions for efficient production of small batches and diverse metal sheet types.
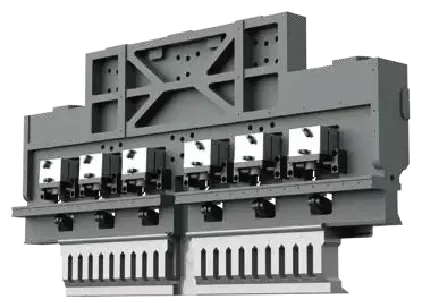
Pneumatic Pressing Tooling
Unique Tooling Change Algorithm: Our exclusive patented algorithm ensures quick and effortless tooling changes.
Efficient Partial Bending: Precision in partial bending achieved through specialized workmanship and assistant tooling.
Ideal for Small Batch Production: Tailored for efficient handling of small batches and diverse metal sheet types.
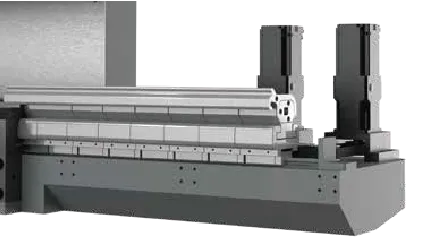
Assistant Tooling
Partial Bending with Customizable Assistant Tooling: Assistant tooling enables precise partial bending, with customizable upper and lower tools to meet specific processing requirements.
Flexibility and Convenience: The system is designed for enhanced flexibility and convenience, ensuring higher efficiency in bending processes while expanding its applicability.
Wide Range of Applications: With its versatility, the assistant tooling system caters to a broad spectrum of applications, providing adaptability across various workpieces and manufacturing
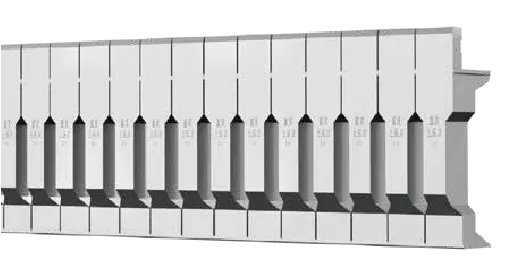
High precision mold
Enhanced Tooling Durability: Combining overall heat treatment and ultra-cryogenic processing results in tooling with increased rigidity and superior wear resistance, ensuring prolonged durability.
Precision with Fanuc Slow-Wire Processing: Leveraging imported Fanuc slow-wire processing technology, our tools achieve higher consistency, reaching tooling accuracy up to the μm level.
Advanced Manufacturing Techniques: Employing cutting-edge techniques, our tools undergo a meticulous process of heat treatment and cryogenic processing, guaranteeing heightened rigidity and exceptional wear resistance for optimal performance.
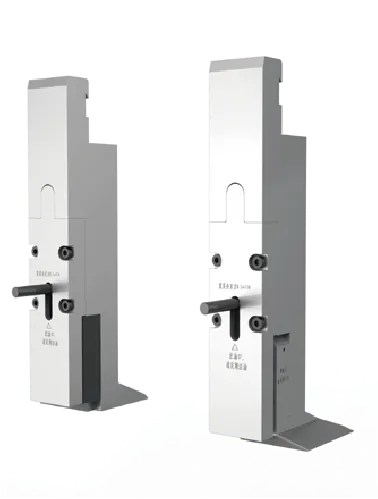
Power Hinge Tooling
Patented Powered Hinge Tooling Technology: Our exclusive patented technology utilizes powered hinge tooling controlled by a full electric servo, ensuring precise and controlled expansion and retraction.
Precision in Power Hinge Tooling Operation: The power hinge tooling is engineered to precisely open without exerting lateral scraping force, guaranteeing accuracy, avoiding material shaving, and preventing scratches.
Advanced Servo Control: Leveraging full electric servo control, our powered hinge tooling technology stands out for its precision, minimizing any undesirable effects during the expansion and retraction process.
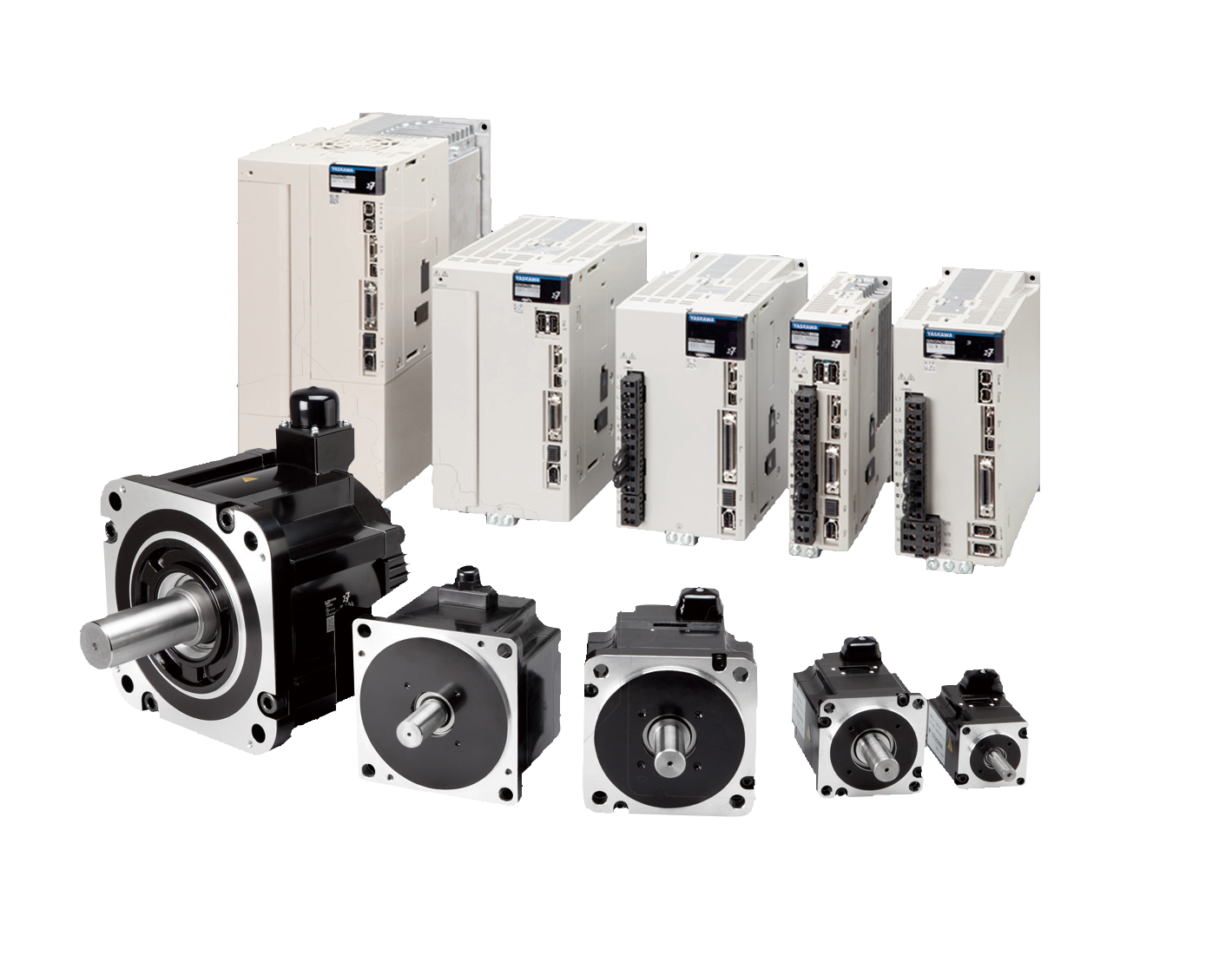
Yaskawa servo motor
Outstanding Performance: Yaskawa servo motors from Japan are known for delivering top-notch precision and efficiency in motion control.
Reliability in Operation: Designed for stability and reliability, Yaskawa servo motors ensure consistent performance in various industrial settings.
Versatility and Adaptability: Yaskawa servo motors demonstrate flexibility and adaptability, making them suitable for a wide range of industrial applications.
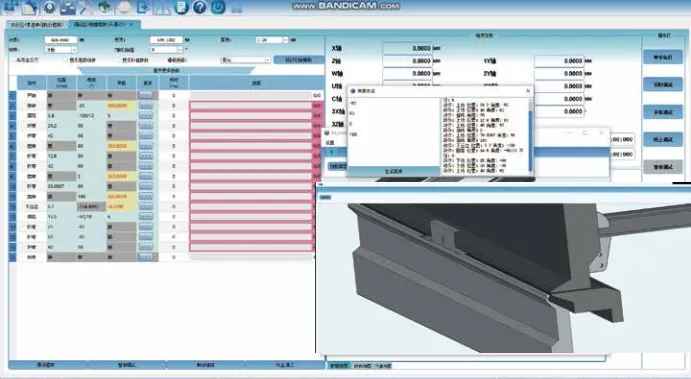
2D/3D drawing import
Intuitive 2D Graphic Programming: Our system offers an intuitive 2D graphic visual programming interface, allowing users to input specific bending parameters effortlessly and generate bending programs automatically.
Effortless Bending Parameter Input: Simplify the programming process by inputting bending parameters directly into the 2D graphic interface, streamlining the generation of bending programs for increased efficiency.
Seamless Integration with 3D Drawings: Enhance versatility with the ability to import 3D drawings directly into the programming interface, providing comprehensive support for a more integrated and efficient workflow.
Let us get in touch with you!
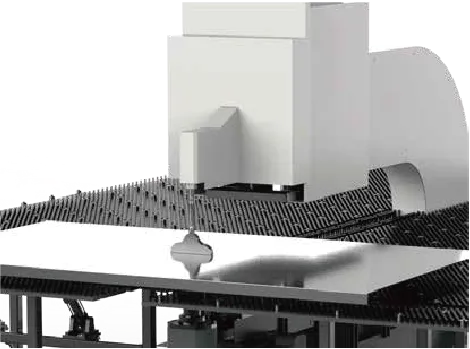
Feeding rotating shaft
Improved Efficiency: The automatic feeding and rotating axis enhance operational efficiency, streamlining material handling and reducing downtime.
Precision Bending: Automated rotation ensures precise positioning, contributing to accurate and consistent bending of metal sheets.
Versatility in Handling: The automated axis accommodates various sheet sizes and shapes without manual adjustments, increasing overall system flexibility.
Need Help?
FAQs
Questions? We've Got You Covered!
Are you a factory or a trading company?
We’re a manufacturer with 20+ years of production experience since 2003.
How long does it take to deliver the machine?
Normally, our delivery timeline is within 25 days. For custom non-standard machines, it might extend, yet never surpassing 45 days.
What kind of payment do you accept?
We generally accept T/T and L/C payments, with a 30% deposit and 70% payment before delivery. However, for special customers, we can offer better payment options.
How does your company provide after-sales service?
We provide remote support by our mechanical engineers for resolving minor issues encountered while using our machines. This includes personalized guidance, offering text instructions or videos as needed. During the warranty, replacement parts are provided at no cost, though local purchases are an option for faster access. In case of more complex issues, on-site service can be arranged if remote guidance isn’t sufficient. For areas with our agents, we directly coordinate service through them.
Where is your company?
Our company, situated in Nanjing, Jiangsu Province, is just a 20-minute drive from Nanjing Lukou Airport. Should you decide to visit, we offer a convenient shuttle service from the airport.
What is the warranty period of your machine?
We provide a one-year warranty for standard machines and extend it to 2-3 years for special non-standard ones. Please verify the warranty duration with our sales team beforehand. Throughout this period, we offer complimentary replacement parts.
How do you ensure the quality of your machines?
We utilize an array of substantial equipment—tempering furnaces, shot blasting machines—for frame durability. Precision is assured through the use of five-axis machining centers, floor boring, and milling equipment. Our standardized processes in machine processing, assembly, and quality inspection ensure meticulous control over product quality at every production stage.
How to ensure that the machine I ordered is suitable for me?
Prior to order placement, our sales team conducts thorough discussions to understand your specific needs. Based on this, we suggest a custom machine configuration tailored precisely to your requirements. Our focus isn’t on recommending pricier options for sales purposes; rather, it’s about ensuring you invest in the most suitable machine for your business.
News & Blogs
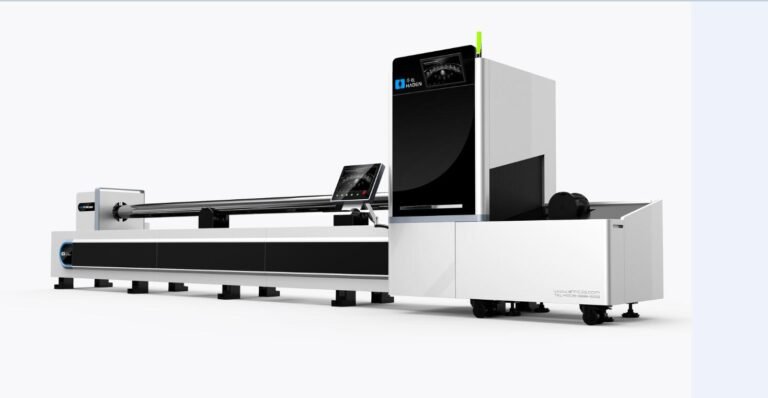
The Benefits of Tube Laser Cutting: Precision, Efficiency, and Versatility
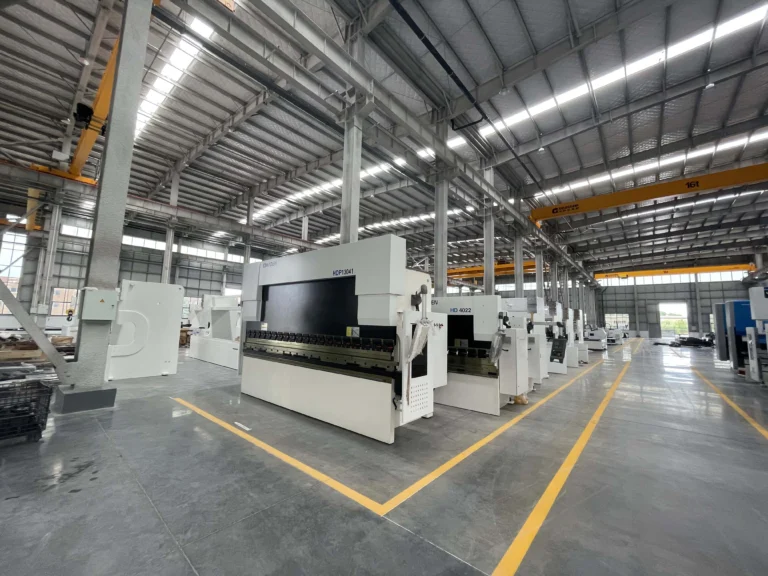
How Haden Improves the Quality of Its Press Brake Machines
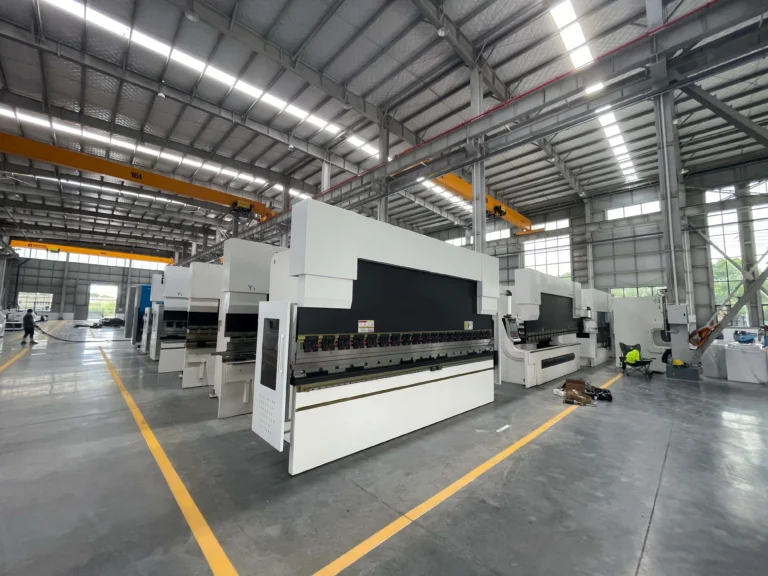