Flex series
- Flex series – Torsion bar synchronous on both side hydraulic oil cylinders.
- The torsion bar brake press machine is the entry-level model for entrepreneurs.
- Suitable for starting a new metal processing business, you don’t want to invest much money.
Configuration
- Standard:Estun E21 NC Controller
- Premium: Estun E310P CNC Controller with Servo Position
Performance
- Positioning Accuracy: ±0.1mm
- Approaching Speed : 90-130mm/s
Business
- Delivery: 5 weeks(common models are in stock)
- Warranty: 1 year for the controller, 2 years for whole machine
Pro Series
- Pro series – High-precision German hydraulic proportional valves rexroth control Y1 and Y2 respectively.
- It is suitable for medium-sized factories that need to improve production efficiency, improve product quality, and have stable business.
Configuration
- Standard: Delem DA53t 4+1axis
- Premium: Delem DA66t/Esa S875 8+1axis
Performance
- With strong anti-eccentric load capability.
- The accuracy is qualitatively improved. ±0.01mm
- CNC performance is greatly improved.
Business
- Delivery: 6 weeks(common models are in stock)
- Warranty: 1 year for controller/rexroth hydraulic system, 3 year for whole machine
Max series
- Max series – Servo motors drive the Y1 and Y2 oil pumps respectively, which directly drive the movement of the hydraulic cylinder.
- It is less affected by oil temperature/oil quality, and its stability is ultimately improved.
- Suitable for automated unmanned workshops with robots and a high degree of automation.
Configuration
- Standard: Delem DA66t/Esa S875 8+1axis
- Optional: Wila punch & die clamp/crowning,DSP/AKAS laser protection,Appearance rendering customization,Sheet follower,Laser angle check. Bending robotic arm.
Performance
7x24h Automated Production
Business
- Delivery: 7 weeks
- Warranty: 1 year for controller/Hawe servo pump control system, 3 year for whole machine
Electra- series
- Electra series -The motor drives with a reducer that directly drives the Y1 Y2 grinding screw.
- All electric CNC press brakes bending machine technology represents the future and technology.
Applicability
- Small precision parts
- Save energy consumption(40%-60%) and reduce production costs
- Special non-hydraulic oil industry
Capabilities
8T200mm – 170T4000mm
Business
- Delivery: 7 weeks
- Warranty: 1 year for controller/Screw, 3 year for whole machine
Let us get in touch with you!
F.A.Q
Our press brakes are divided into two types,4 series: hydraulic and fully electric – Electra. The hydraulic series are further broken down into three categories: Flex, Pro, and Max, each offering different levels of performance and precision.
[Learn More About Haden Press Brake Series]
- We ensure alignment in service philosophy.
- We assess your company’s strength. The requirements may vary depending on the market.
[Apply to Become a Dealer]
Of course! Contact us to arrange a visit. We provide free airport pickup, accommodation, and meals during your stay.
[Schedule a Factory Tour]
Selecting the right press brake depends on factors like your material type, thickness, desired bend precision, and production volume. We recommend consulting with our experts to determine the best solution for your needs.
[Get Help Selecting Your Press Brake]
The accuracy of our press brakes comes from high-quality components, precise synchronization systems, and advanced control software. Each part of the machine is fine-tuned to ensure optimal performance.
[Discover More About Press Brake Accuracy]
Yes, we provide customized, OEM, and ODM press brake solutions. Additional charges apply based on the level of customization.
[Inquire About Custom Press Brakes]
Both our Sales Director and Technical Director have over 30 years of experience in the industry. Since producing our first CNC press brake in 2009 (which is still in our showroom), we’ve committed to delivering top-quality machines. We also offer comprehensive industry solutions to meet customer needs.
[Learn More About Our Quality Assurance]
We provide a 3-year warranty on the entire machine and a 1-year warranty on imported systems. Our standard delivery time is around 4-5 weeks, though we often have semi-finished or ready-to-ship models available.
[Get Details on Warranty and Delivery]
Our machines are positioned in the mid-to-high-end market, balancing quality and cost-effectiveness.
[Request a Quote]
We generally do not offer discounts unless we are supporting a dealer with significant potential. In those cases, we are willing to share some of our profit to help them grow.
[Discuss Dealer Opportunities]
We are a factory. Our Sales Director and Technical Director both have over 30 years of industry experience. Since producing our first CNC press brake in 2009, we’ve continued to innovate. We also provide complete industry solutions.
[Learn More About Haden]
If you have any questions, comments or suggestions, please feel free to let us know. info@hadenfab.com
Main details
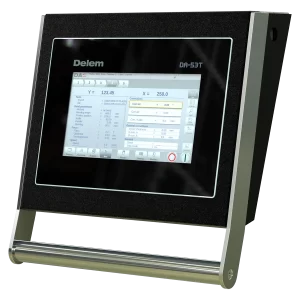
CNC Hydraulic press brake
Delem DA53t
- “Hot-key” touch navigation
- 10.1″ high resolution colour TFT
- Up to 4 axes (Y1,Y2 + 2 aux. axes)
- Crowning control
- Tool / material / product library
- Servo and frequency inverter control
- Advanced Y-axis control algorithms for closed-loop as well as open-loop valves.
- TandemLink (option)
- USB memory stick interfacing
- Profile-T offline software
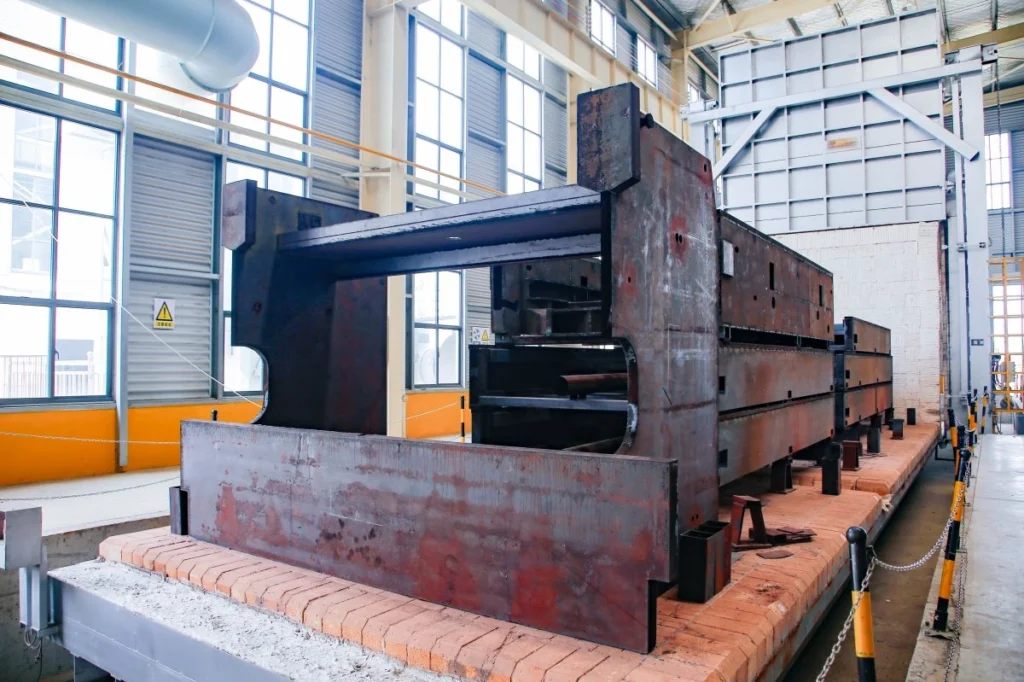
Machine Bed & Machining
- Precision in the bed is ensured through meticulous machining.
- Comprehensive annealing of the entire machine is crucial to minimize deformation and guarantee accuracy.
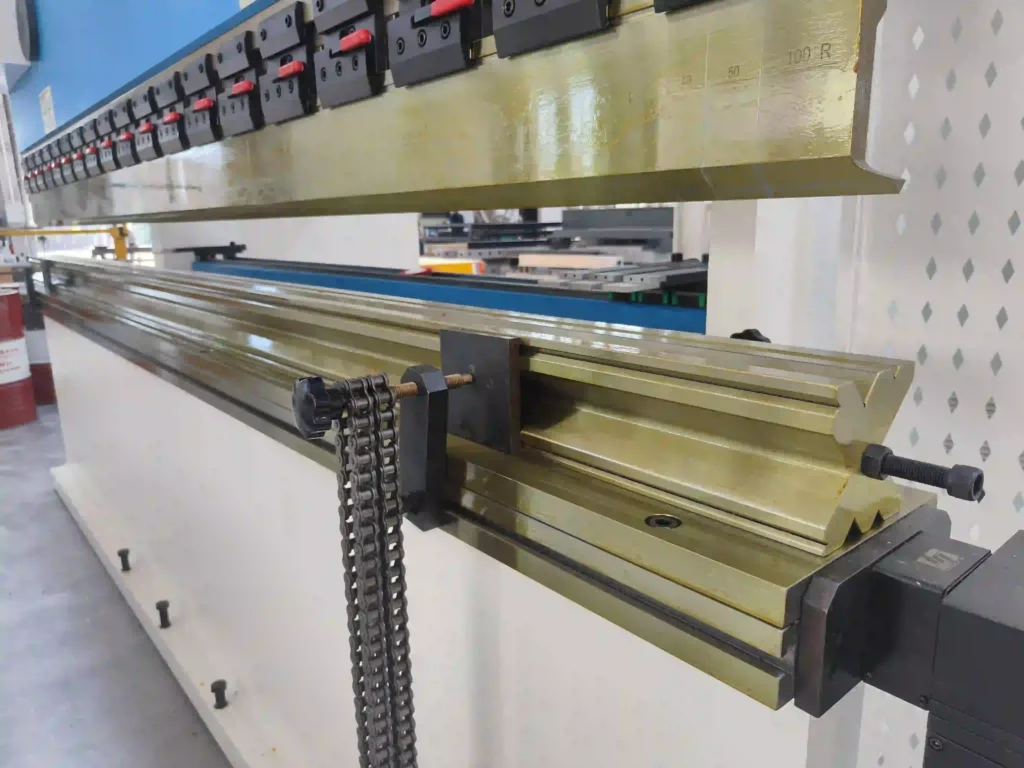
Multi - V Die
- Uniform Bending Across Length: The double V-shaped concentric tooling ensures uniform bending along the entire length of the workpiece, minimizing inconsistencies and improving overall accuracy.
- Increased Stability: The concentric design of the double V tooling enhances stability during the bending process, reducing the risk of deflection and resulting in precise and reliable bends.
- Versatile Application: Dual V-shaped tooling provides versatility, allowing the CNC press brake to handle a wide range of materials and thicknesses, making it suitable for various bending applications.
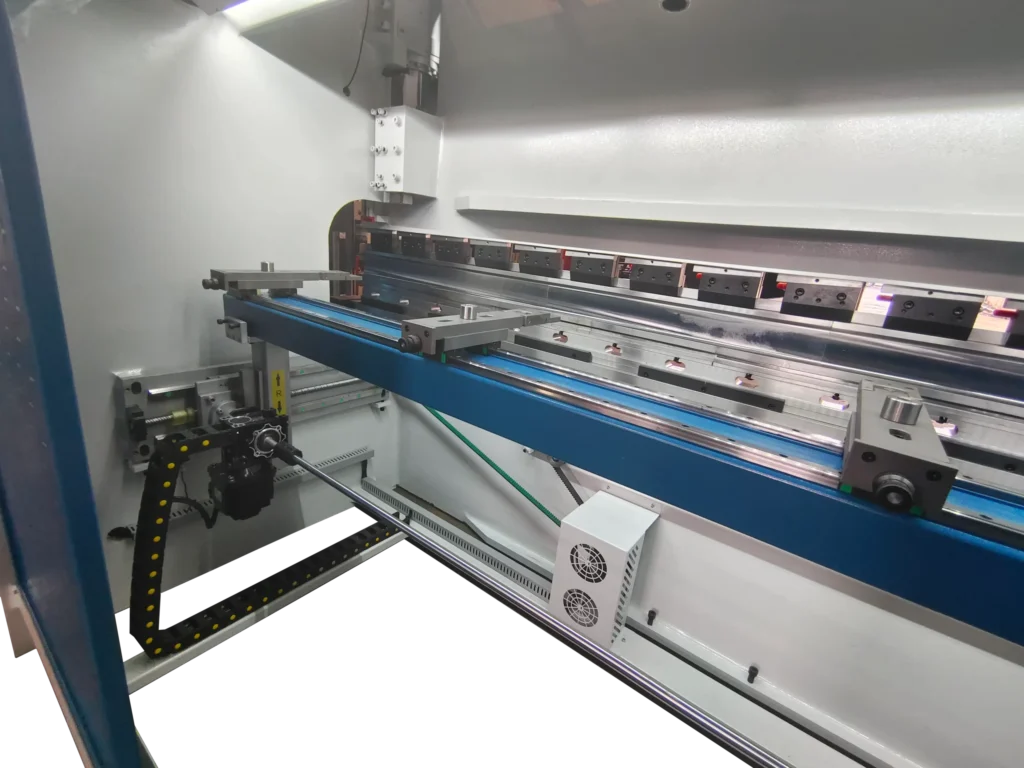
Control Axis 4+1: X Y1 Y2 R
Enhanced Precision: The 4+1 axis configuration in the CNC press brake allows for increased precision and intricate bending operations.
Versatile Bending Capabilities: With four primary axes for movement and an additional rotary axis, the machine gains versatility, enabling the bending of complex and multi-dimensional parts.
Improved Efficiency: The integration of a 4+1 axis system enhances operational efficiency by reducing the need for manual adjustments, resulting in faster and more accurate bending processes.
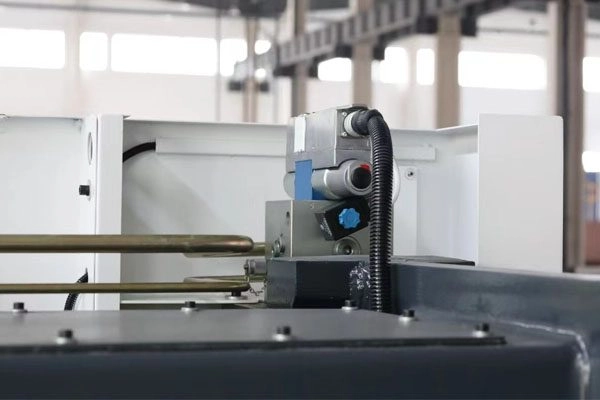
Bosch Rexroth
Hydraulic System
- Cutting-Edge Technology: Bosch Rexroth valves feature advanced technology for precise fluid control, ensuring top-notch performance.
- Robust and Durable: Known for their durability, Bosch Rexroth hydraulic valves are designed to withstand demanding industrial conditions, requiring minimal maintenance.
- Industry-Leading Expertise: Benefit from Bosch Rexroth’s extensive hydraulic system expertise, delivering valves that meet or exceed industry standards for optimal
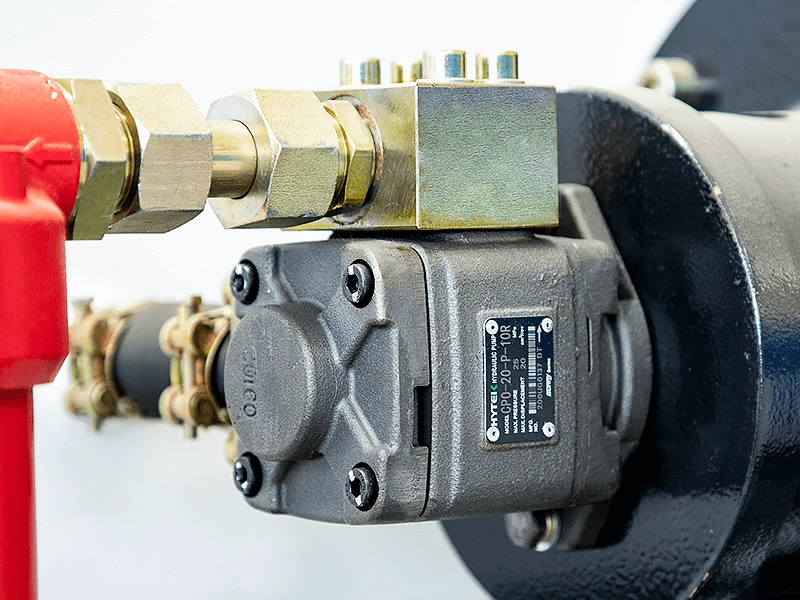
Sunny Hytec Oil Pump
Efficient Hydraulic Power: A quality oil pump ensures efficient and reliable hydraulic power, essential for the optimal functioning of the press brake.
Consistent Bending Performance: The proper functioning of the oil pump contributes to consistent and stable bending performance, maintaining accuracy and repeatability in sheet metal processing.
Enhanced Machine Productivity: A reliable oil pump plays a crucial role in maximizing the productivity of the press brake, facilitating smooth and precise bending operations over extended periods.
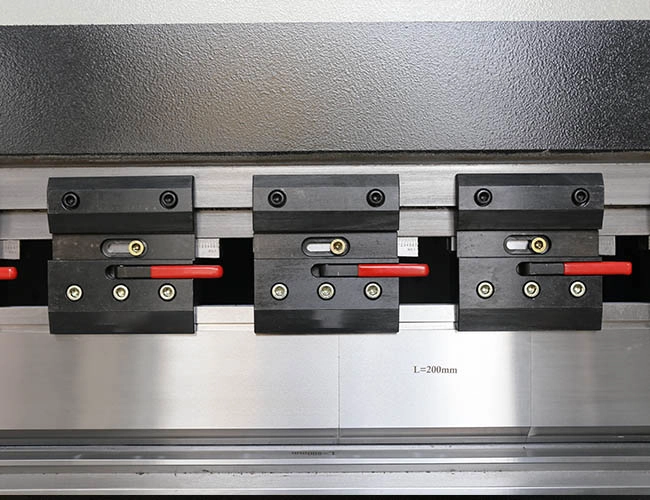
Quick Clamp
- Rapid Setup: Swift changeover between different bending applications minimizes downtime.
- Increased Productivity: Reduces tooling adjustment time, boosting overall sheet metal bending efficiency.
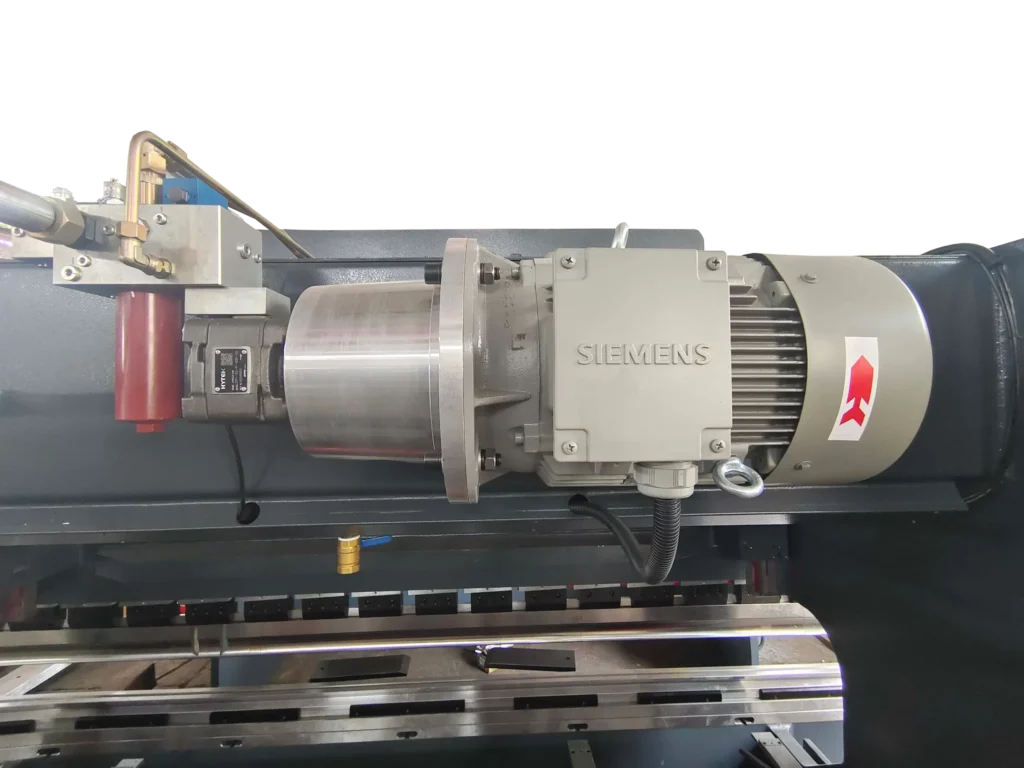
High-efficiency Siemens main motor
Reliable Siemens Motors: Our NC press brakes feature Siemens main motors, known for their reliability and durability.
Precision Bending: Benefit from the precision and consistent performance of Siemens motors, ensuring accurate control in the bending process.
Advanced Integration: The main motors seamlessly integrate with CNC systems, enabling efficient and precise bending operations.
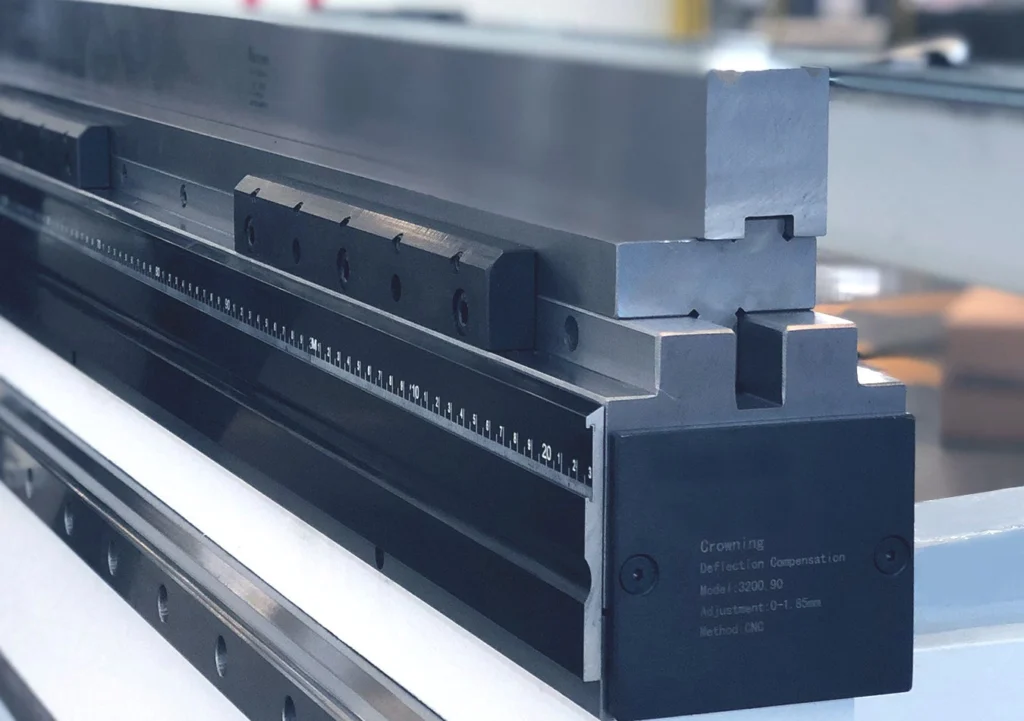
Electro mechanical compensation workbench
- Uniform Bending: The Manual-Crowning feature ensures consistent bending across the workpiece.
- Enhanced Accuracy: Precise adjustments improve bending accuracy and reduce errors.
- Versatility: Adapt the crown settings for a flexible solution with various materials and thicknesses.
Optional Configuration
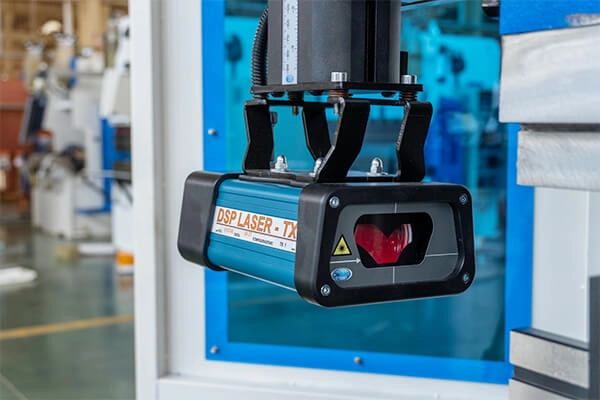
DSP laser protect device
Enhanced Safety: DSP laser protection ensures a secure work environment by swiftly stopping the hydraulic press brake upon detecting obstacles in the laser path.
Precision Alignment: Accurate positioning of the laser beam guarantees that the protected area aligns precisely with the intended work zone, minimizing the risk of accidents and equipment damage.
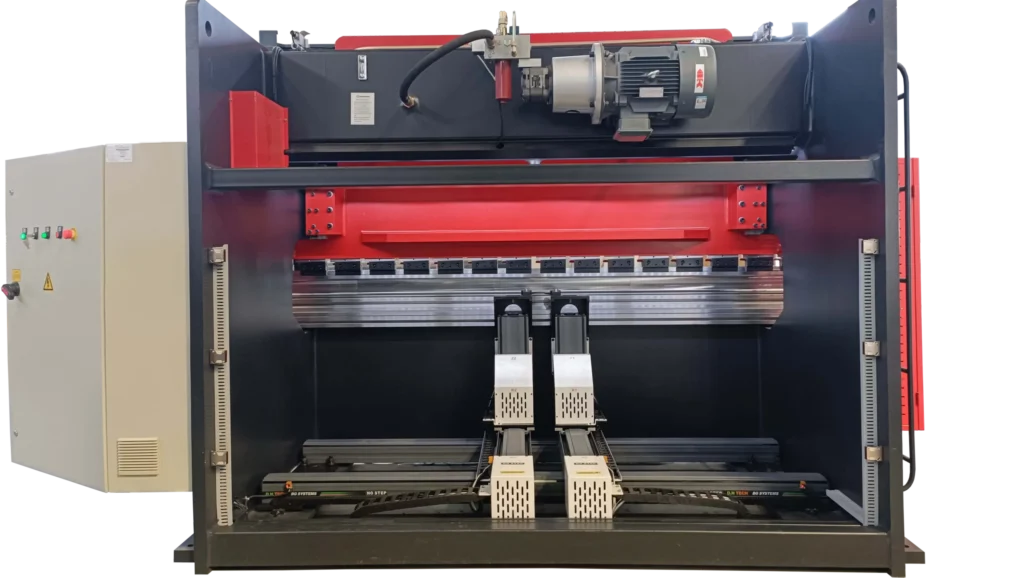
6 Axis Servo Control Backgauge
Precision Positioning: The 6-axis servo control backgauge enables accurate and reliable positioning of the sheet.
Versatile Movements: With independent control over multiple axes, the backgauge provides flexible and adaptable movements to meet various bending needs.
Consistent Accuracy: The servo system ensures consistent precision, contributing to reliable and repeatable bending processes.
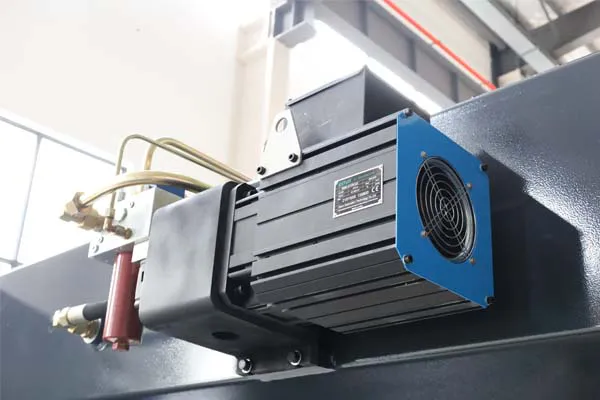
Main servo motor
Precise Motion Control: The main servo motor in a CNC bending machine is responsible for precise and controlled movement, allowing for accurate positioning of the bending tools.
High-Speed Operation: This servo motor enables high-speed operation, contributing to efficient and quick bending processes, which is crucial for improving overall productivity.
Energy Efficiency: The main servo motor is designed for energy efficiency, ensuring optimal power usage during various bending operations and minimizing energy consumption.
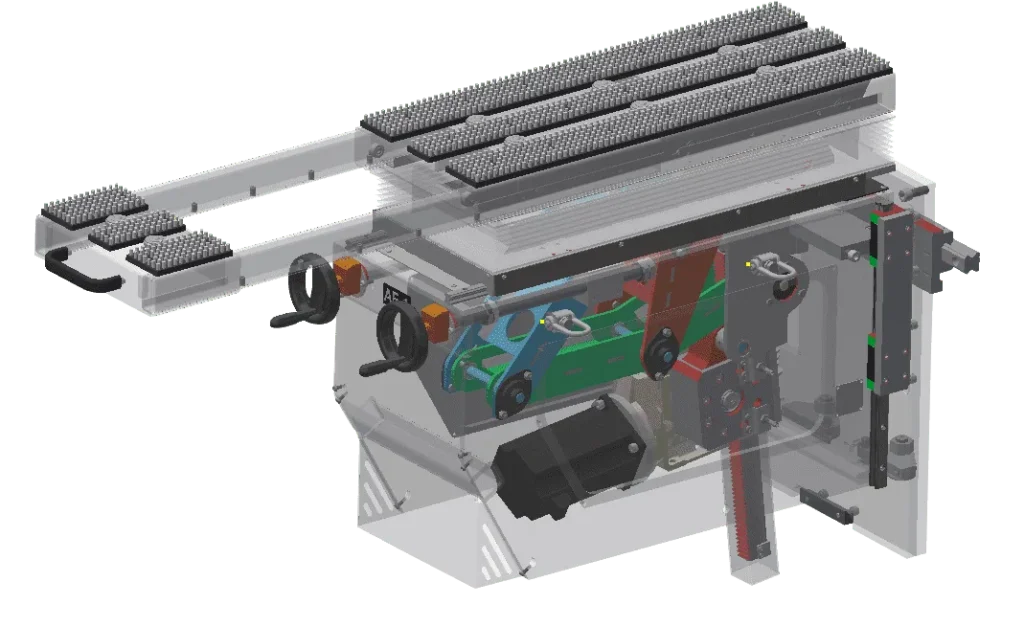
Sheet Follower Front Support
Enhanced Stability: The Sheet Follower Front Support ensures increased stability for the sheet metal during bending, minimizing the risk of deflection.
Improved Precision: By providing additional support, this feature contributes to enhanced bending accuracy, ensuring that the sheet is precisely formed according to the desired specifications.
Optimized Quality: The support system helps maintain consistent and reliable results, especially when working with larger or heavier sheets, ultimately leading to higher-quality finished products.
Processing equipment
- Our hydraulic NC&CNC press brake epitomizes our manufacturing prowess, seamlessly blending technology and craftsmanship.
- With precision and efficiency, this cutting-edge machinery showcases our commitment to high-quality metal fabrication, reinforcing our industry leadership.
News & Blogs
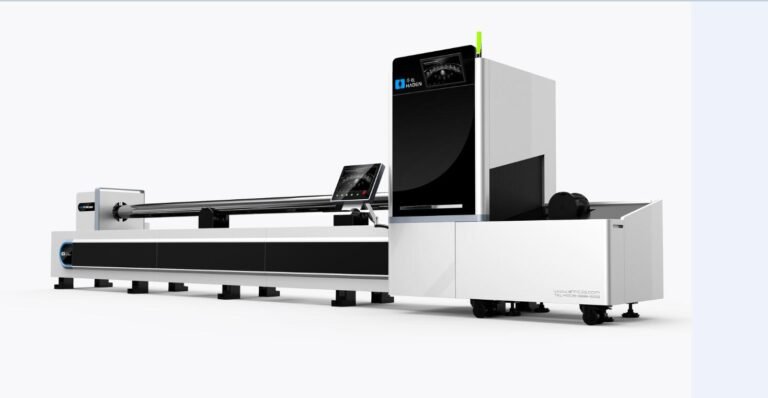
The Benefits of Tube Laser Cutting: Precision, Efficiency, and Versatility
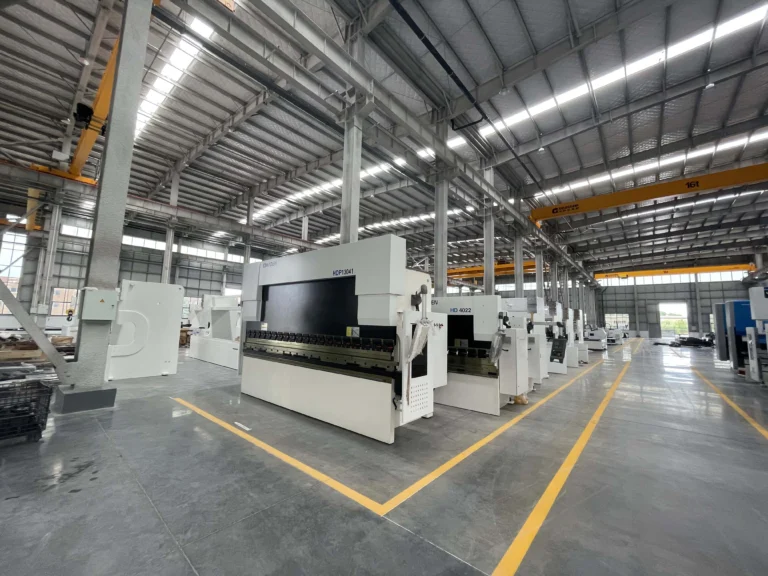
How Haden Improves the Quality of Its Press Brake Machines
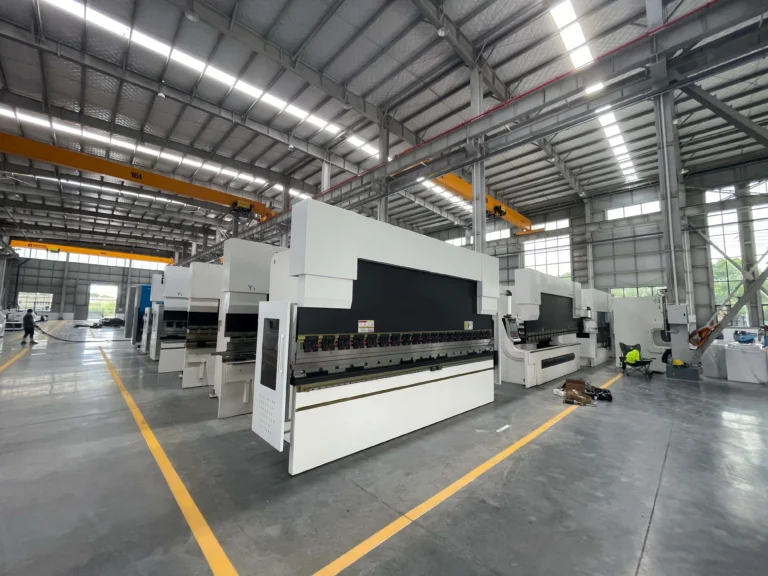